Diving into Design: Conceptual Design - Part 1 - Technology Trade-offs
Attempting to balance the benefits and drawbacks of novel technology choices
Hello again, I’m back after a slightly shorter gap this time, with the start of hopefully what will become a series of posts on the design process. As always, I’ll caveat with the fact that I’m learning this as I go, so if something seems off, then do let me know – I’m always keen to learn, and this is very much an iterative process!
A Quick Recap
I wrote about the early design process a while back, but it’s been a while, and my understanding has improved somewhat since then, so let’s recap the broad strokes of the design process.
At a high level, aircraft design generally falls into three main phases: conceptual design, preliminary design and detail design. Conceptual design is what it sounds like – once a market has been determined and initial requirements are in place, a number of concepts are drawn up to try and fit those requirements. None of these are anything close to final, but the idea is to figure out the various trade-offs between broad design choices, and iterate between what’s possible, the risks involved and what the customers want. Usually several different configurations will be prepared, then studied at a high level, with trade studies and discussions with customers and various specialists in different domains.
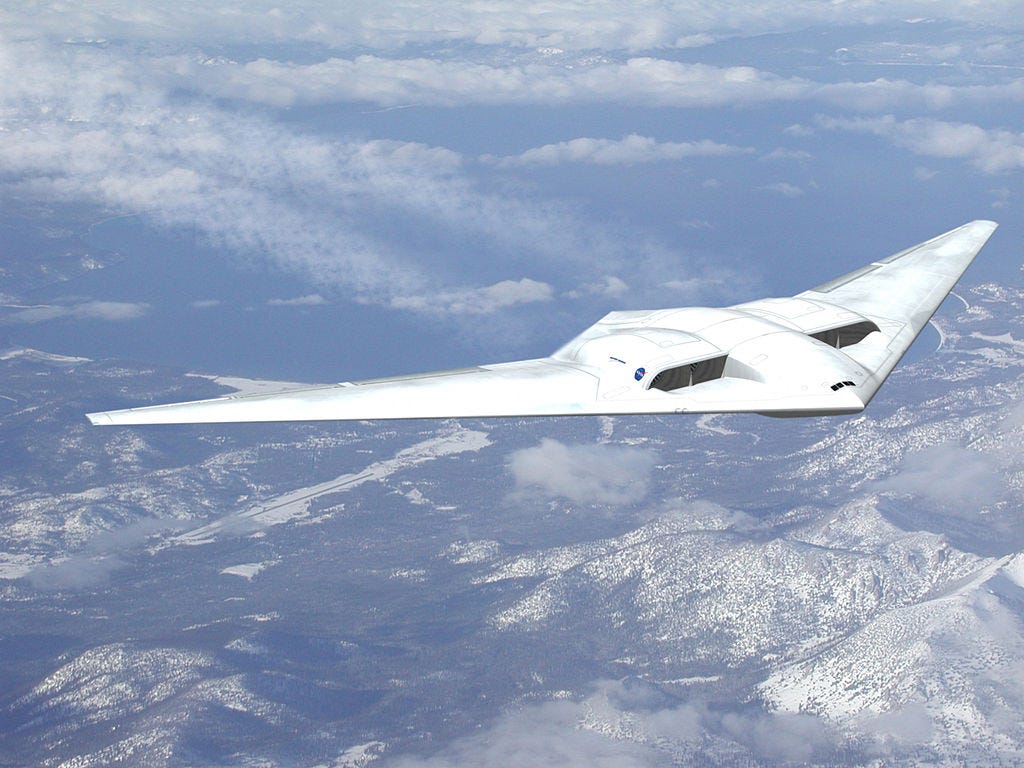
Ultimately, one concept will be chosen, locking in the broad parameters of the design – how many engines, what the wings look like, does the aircraft have canards, etc, along with a host of other decisions. At this point, preliminary design begins. The overall design is ‘frozen’, and each area is analysed in much more detail – aerodynamics, structures, control systems and more. Everything is fitted together, and all of the performance worked up thoroughly, and adjustments made. Once all major systems appear to be working together as they should, then the aircraft is moved to detail design.
Detail design is basically everything to get the aircraft to manufacture – every component is worked up, fitted together, all wires, components and systems figured out and made manufacturable. The end product of this phase is a complete aircraft, which can then be built, assembled, tested, flown and (hopefully) eventually certified.
The overall structure of the design process is like a funnel, where as you go further down, more and more about the design is locked in place, and the more rigorously everything is checked, analysed and specified. This means that whilst most of the work is done in the later stages, the decisions made in the conceptual design stage massively influence everything that comes later. As such, conceptual design needs to consider ramifications of design decisions on everything from costs to manufacturability and repair.
Risk and novel technologies
I’ve talked before about the need to innovate, and how risk averse aviation is (for good reason!). I think there’s a pressing need to innovate more radically, especially in light of the ever-heightening climate crisis, but even then, we still need to consider each technology inclusion carefully, and not just throw in every shiny new idea that looks somewhat relevant. Every choice needs to justify its place on the aircraft!
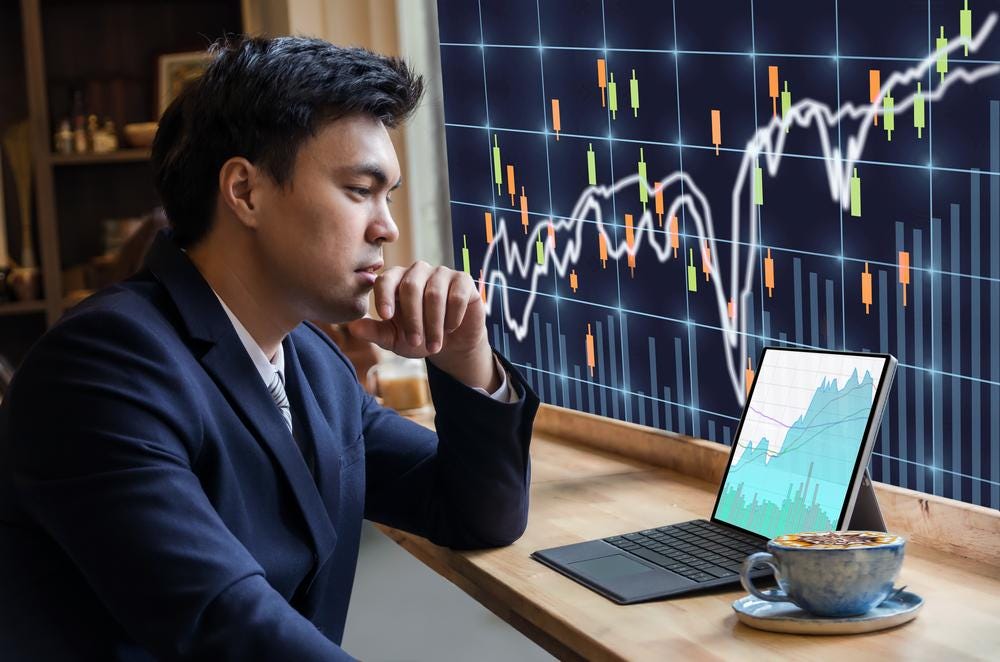
This is true not only from an engineering perspective, but also the business side. Every decision is a balance between the benefits given and the drawbacks from its inclusion. New or unproven technology may offer large potential gains, but also brings risks, uncertainty and expense alongside purely technical limitations. New tech requires proving out and testing to quantify its behaviour – both the benefits it brings but also how it changes the aircraft, from weight to manufacturing to safety.
The ultimate expression of this is certification – every part of an aircraft needs to be approved by regulators as safe to fly, and any novel technology will need to be thoroughly understood and quantified, and any safety concerns addressed thoroughly. This is not a cheap nor a short process, and a risky technology could add years and hundreds of millions to the development process. Making the aircraft more efficient is great, but not if the additional certification requirements and testing make the company run out of money!
Clearly we need to find the middle-ground – a technology roadmap that balances risk with reward, and where the risks and trade-offs of each choice are clear, and ideally mitigated in some way. Thus, a good starting point is to line up all the potential technology choices and analyse them. What benefits do they bring? How proven are they? Do they depend upon another technology (or unlock the ability to use another)? Is there a more well-understood alternative, and what is the trade-off should that be chosen?
Building a Foundation
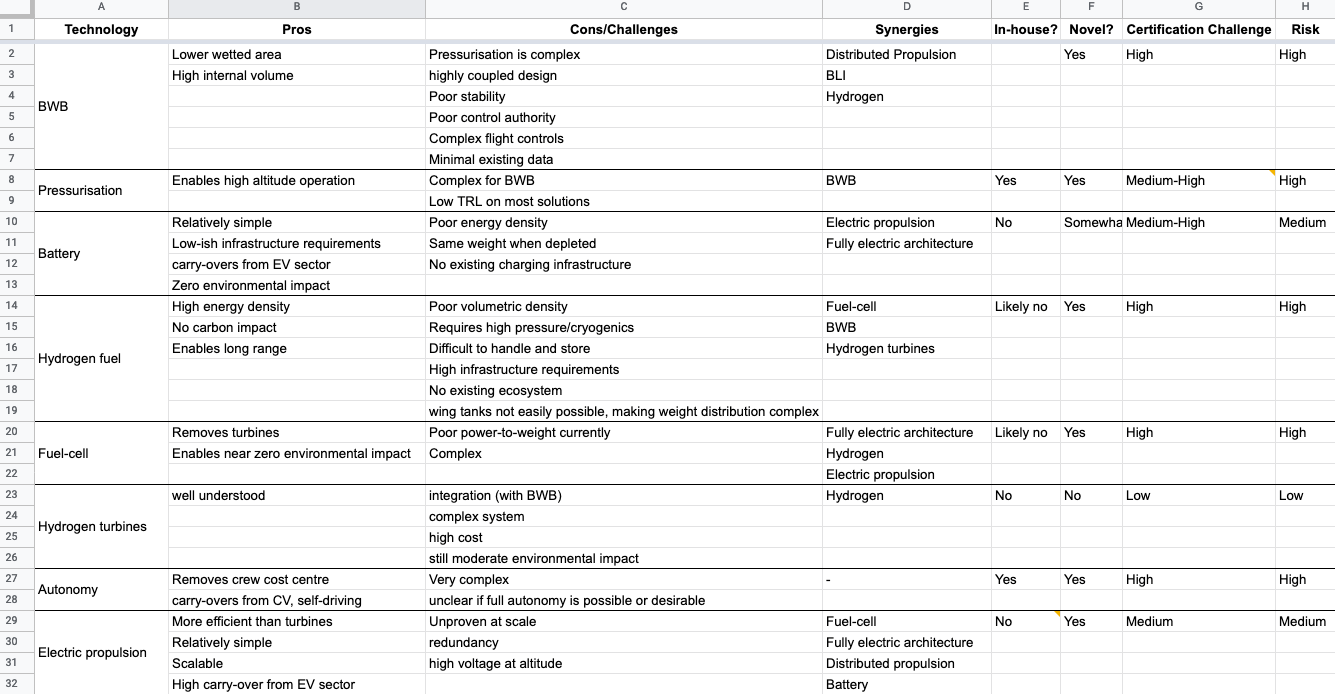
This becomes more clear with concrete examples. Here on The Raven, I’ve been examining blended-wing body (BWB) designs extensively, so let’s start there. As I’ve touched upon previously, they offer various potential benefits, including lower drag and higher internal volume, but also significant downsides – complex flight controls, difficulty with pressurisation, poor pitch control, and more.
However, deciding whether the BWB is a good answer for an aircraft design requires more context. The BWB is ultimately a carrier for all the many other systems that make up the aircraft, from propulsion to airframe material, and the choices made in designing those subsystems can simplify the development of the BWB design or make it virtually impossible.
To look at energy storage – if zero-emissions is our goal, we have batteries and hydrogen. We have to weigh up the limitations of battery systems (the high weight and inherent short range) against the benefits of a simpler and more mature architecture versus, say, hydrogen. That being said, nothing in the battery electric chain is yet certified, and there’d have to be a choice as to whether to delegate complex components like batteries and motors to outside parties, and what the risks are there.
A battery energy source also locks in a motor-based propulsion system, which in turn needs R&D, certification, all of which adds to cost and complexity. Obviously, this could be a more conventional system such as that being used by Heart Aerospace, in which case the route to certification looks more straightforward, or it could be more novel, like Lilium’s tilting distributed ducted fan system, which also functions as part of the flight controls. Each needs weighing up as part of the whole package.
Hydrogen on the other hand offers superior range and lower weight, but a different set of challenges. Tanking hydrogen is complex, whether as a pressurised gas or in liquid form, and relies on a whole new fuel infrastructure being developed and rolled out. Companies like Universal Hydrogen and ZeroAvia are biting off bits and pieces of this puzzle, but all are early efforts, and there’s a long road to travel before solutions will be flying commercially and rolled out at major airports. However, hydrogen keeps more options open in the propulsion chain, as hydrogen can either be burned in a conventional (albeit modified) gas turbine, or consumed by a fuel cell for an electric propulsion system.
Thus, we can start to map out the various potential technology choices and dependencies, and see what’s risky and what’s not. This then informs our roadmap – if we know where we want to end up, we can hopefully figure out a pathway that incrementally adds novel technologies, rather than a big bang, all-in-one approach. This is the only real way to introduce serious novelty whilst still keeping risk at a reasonable level – an essential requirement for a business that needs to raise major capital to get anywhere.
Next steps
This technology roadmap and technology trade-off study is one of the building blocks for understanding what an initial aircraft might look like (even if it doesn’t immediately seem like it). It allows us to start working up a host of different concepts, from the conventional to the radical, assessing not only performance against likely market requirements, but timelines and risk profiles for development and funding. Aircraft design and development is all about trade-offs, and this is no different – we need to balance risk and reward, not just blindly placing our bets on the technology that seems most likely or exciting, as tempting as that may be!
In the case of my work here, that means figuring out if a blended-wing body truly will give the benefits I hope it can to a zero-emissions aircraft concept, and whether such a design is worth the development risk. Given the novelty of BWB designs, we also need to figure out how different approaches to the blend-wing paradigm play out – is it worth going with a fully blended approach, or adopting something more incremental, keeping a more conventional tail and propulsion layout for an initial design, then adding in more radical ideas later?
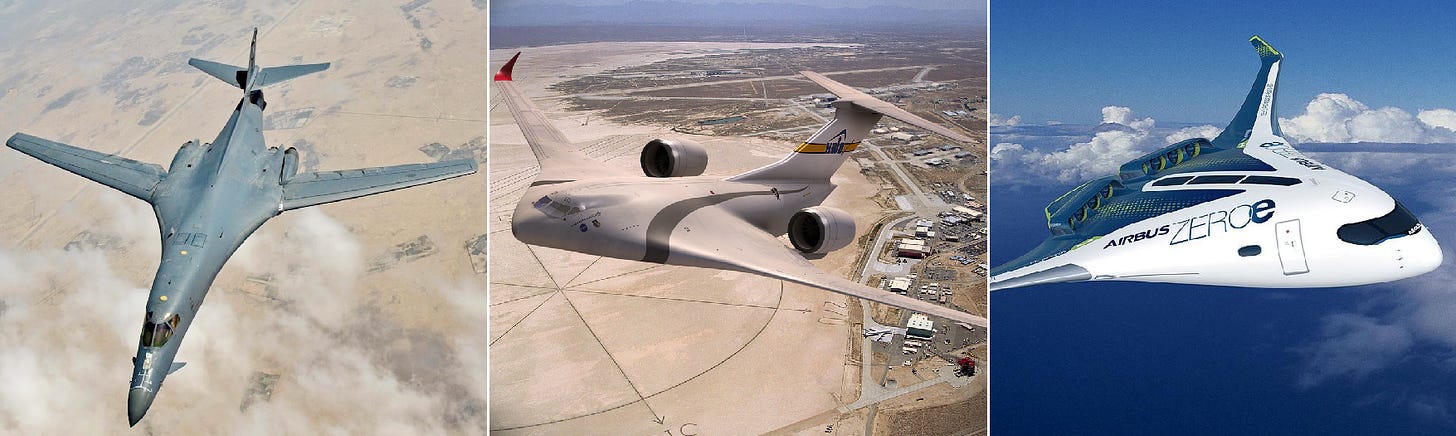
This is going to require a lot of iteration and trial and error, and I’ve been gradually working on various software tools to try and speed up and automate the process between developing an idea and assessing its potential. Going off the beaten track means carving a new path through the jungle, but hopefully with modern, software-driven approaches, it is possible to push further into the unknown whilst still producing a proposition that’s achievable in the current aviation and startup ecosystem.
I’m in the process of a deep dive into conceptual design, and I should be able to talk more soon about what goes into developing and assessing a design at the conceptual stage. As with everything in aerospace, it’s more complex and involved than you might imagine!
If you made it all the way to the end, good job! Thanks for reading – I’d love to know what you think, and I’m always up for talking more about this. If you want to chat or give feedback, please do reach out!
Cheers,
Oli